Engineering
By fusing artisanal skills and advanced IT technology, J-MAX aims to attain “the world’s fastest die manufacturing,” continuously meeting the challenges of manufacturing products that satisfy users around the world.
As the challenge to manufacture next-generation products has begun, J-MAX’s molding technology, which maximizes the advantages of digital engineering, combines its technology with IT to develop its original design and analysis technologies.
Forming technologies for super high tensile materials
Aiming for the ultimate in super high tensile steel plate forming technology
Environment surrounding the automotive industry
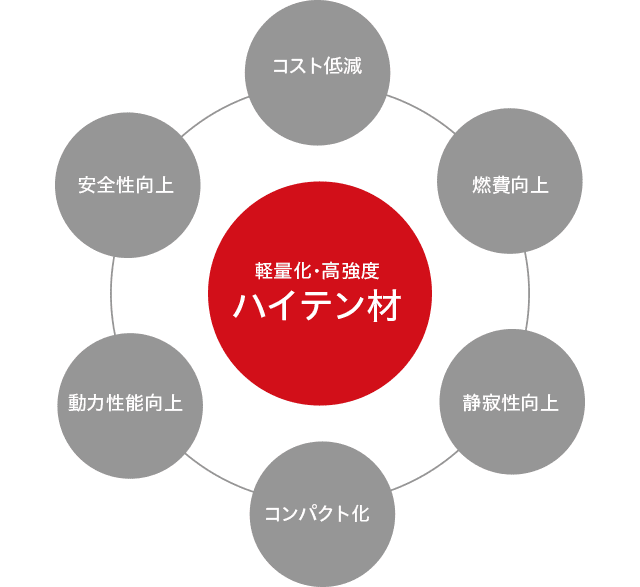
Development of fuel-efficient vehicles that are eco-conscious is proceeding in the automotive industry.
The transition
to super high tensile materials that contribute to making cars lighter and auto bodies stronger has
become an
indispensable theme.
J-MAX is conducting a wide range of R&D including on the processing of super high tensile materials.
What is super high tensile material?
-
This refers to high tensile strength steel plate.
- Ordinary steel plate has a tensile strength of 270MPa, whereas high tensile strength steel is 590-780MPa, and super high tensile strength material is generally 980MPa or higher
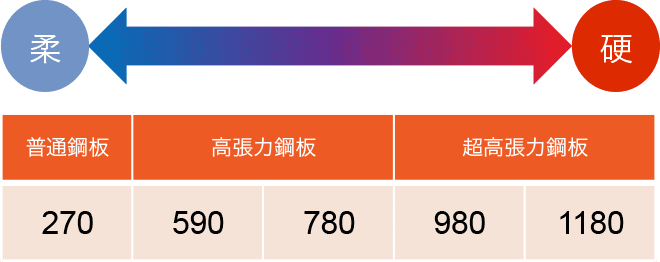
Advantages of super high tensile material
-
Contributing to collision safety and weight reduction
- High tensile materials after stronger than ordinary steel plate and thus improve collision safety. In addition, the use of stronger materials enables plates to be thinner than with conventional materials. The properties of high tensile materials have the potential to improve vehicles’ collision safety and fuel efficiency and therefore these materials have enjoyed increasing adoption in recent years.
Disadvantages of super high tensile material
-
High strength makes press forming difficult
-
- ・Given low ductility, breakage readily occurs so it is necessary to optimize the product form and forming method.
- ・Spring-back is substantial because the form is not conducive to cooling, so a forming method that suppresses spring-back volume is needed.
- ・The forming load of the press is large, so large-scale press facilities and dyes with high strength and stiffness are required.
Differences in approaches to creating high-tensile steel depending on manufacturing method
- Cold-forming manufacturing method for high-tensile steel
- The form is shaped by sandwiching it in the dye (no heating and cooling)
- Hot stamp manufacturing method
- The steel plate is heated to 900°C and the form is shaped by sandwiching it in the dye while cooling.
Productivity | Environment | Cost | Weight | Forming difficulty | |
---|---|---|---|---|---|
Cold-forming press | ○ | ○ | ○ | ○ | Hard |
Hot stamping | × | × | × | ○ | Easy |
Apart from the difficulty in forming, the cold forming of super high tensile materials offers advantages over hot stamping. Difficulty in forming can be overcome by the original technologies that J-MAX has built up since its foundation. Going forward, J-MAX will contribute to the needs of its customers and the environment by evolving and building on its cold forming of super high tensile forming technologies.
Development of ultra-high tensile technology using cold-forming presses
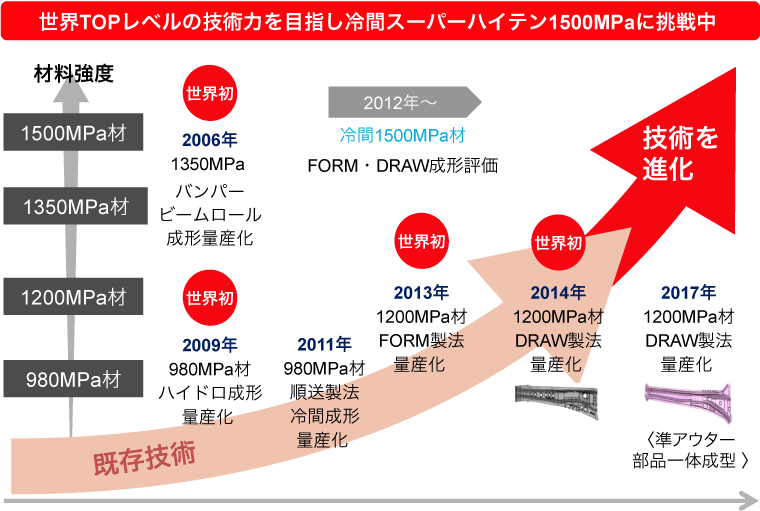
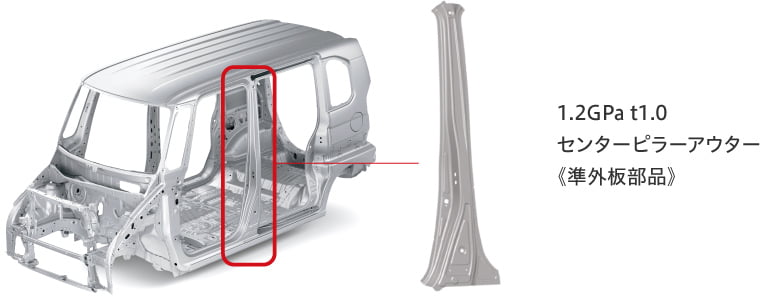
World’s first 1.2GPa-grade super high tensile material used in semi-outer center pillar
-
Achieved through computer simulation technology and long-standing technical know-how of master craftsmen
- The center pillar is an external plate part that is visible to customers when they open car doors, so
they must have a
high-quality appearance that is free of wrinkles and warping.
J-MAX has evolved computer simulation technology to forecast the finished look of products made from materials that are difficult to form. In addition, we were able to use our long-established know-how in dye craftsmanship and original forming technology to suppress the substantial spring-back that super high tensile material is known for.
Process Design Technologies
J-MAX engages in process design for products using forming
simulations and its know-how in the properties of super
high tensile materials.
Since high tensile materials are difficult to process and form, we consider the combination of each process
(drawing,
trimming, bending, etc.) to match the product’s properties.
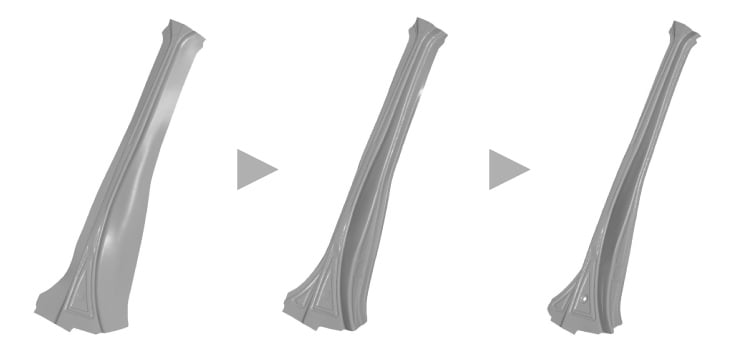
What is forming simulation?
A virtual model is created from product form data, then cracking, wrinkling, warping, and spring-back are analyzed after recreating the press forming process. We have made forecasting possible by creating a database of human knowledge and technology and integrating it with the latest simulation technology to analyze and anticipate product defects with computers in a way not possible in the past.
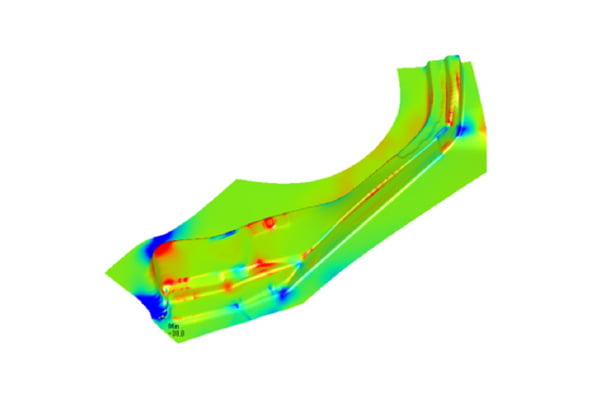

If breaking, wrinkling, bending, or spring-back arise, the virtual model is improved and these defects are analyzed once again. Repeating this process results in rapid dye creation without waste.
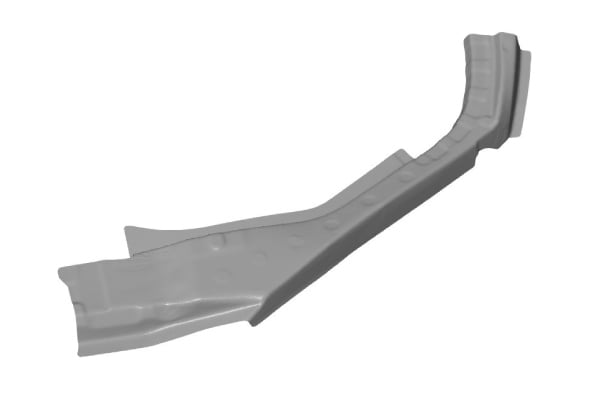
Evaluation by contactless measurement
The dye or product to be measured is converted to 3D data with camera-equipped measuring equipment. The entire object can be viewed instantaneously enabling fast fine-tuning of dyes.
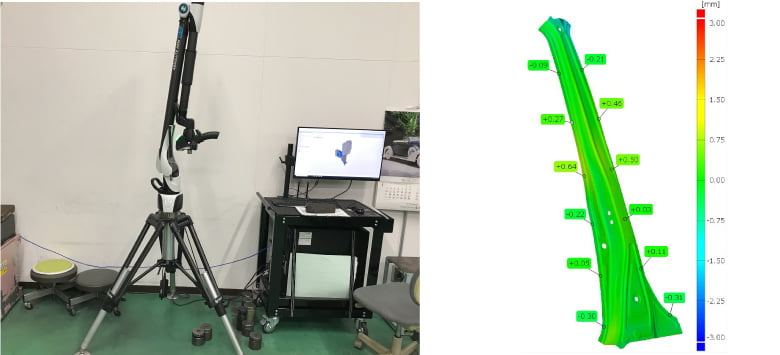
Dye technology
We provide the optimal dyes for all manufacturing equipment thanks to advanced manufacturing technological capabilities built up over many years through IT and mass-production quality that was earned customers’ trust. We assure this through the skills of master craftsmen raised from our talent development.
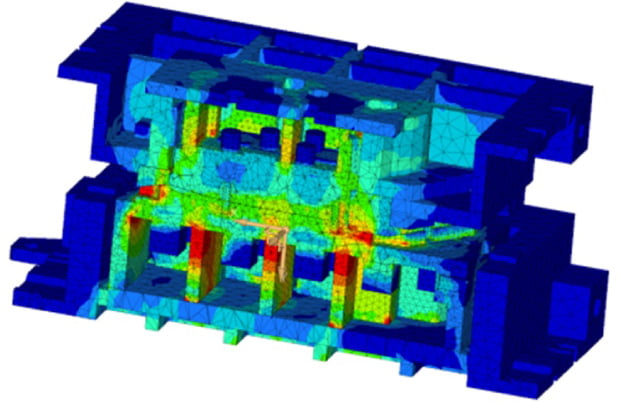
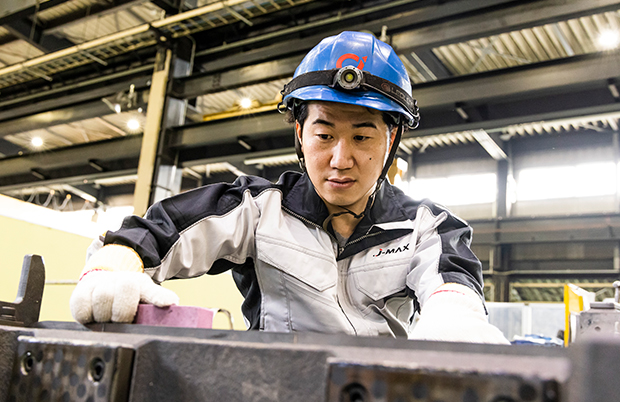
Precision technologies
Processing Technology for Precision Parts
-
Tolerance range by part*
-
Part Tolerance range Processing method Auto body part ±0.1mm unit Press processing (press machinery) Precision part ±0.01mm unit Cutting processing (NC lathes, etc.) ※製品寸法の許容範囲Auto body part Tolerance:±0.1mm unitPrecision part Tolerance:±0.01mm unit
-
Features by processing method
-
Processing method Features Cutting processing Highly precise processing is possible, but requires more time than press processing Press processing Difficult to achieve the precision required in precision parts, but processing time is faster than cutting processing
Thickening process technology
J-MAX has established thinking process technology based on form analysis that can thicken materials by up to 2.5 times through the use of cold pressing forming of products.
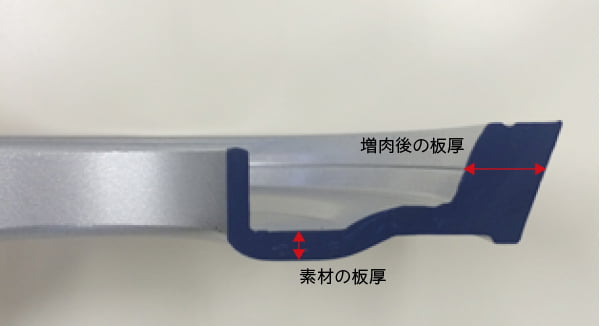