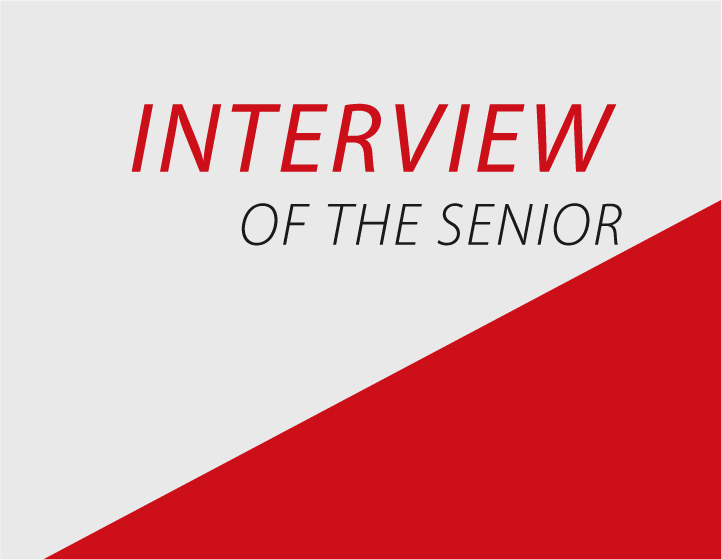
先輩の声
-
自分が調整した金型で
精度の良い製品が
プレスされた時、
この仕事へのやりがいが
湧いてきます。金型製造 T さん
(2013年4月入社)
機械ではできない、
金型の繊細な仕上げ
営業から依頼のあった金型のオーダーを社内で設計し、機械加工を行い、実際に金型ができてプレスできる状態になってからの確認と調整を行っています。お客さまが求める品質になっているかどうかを見極める、最終工程。検具を使って求める長さ、形状に、ぴったりできているかを確認し、仕上げは私たちが行います。金型は機械加工でできるので、100分の1mmのような細かい調整には人の手が必要になります。
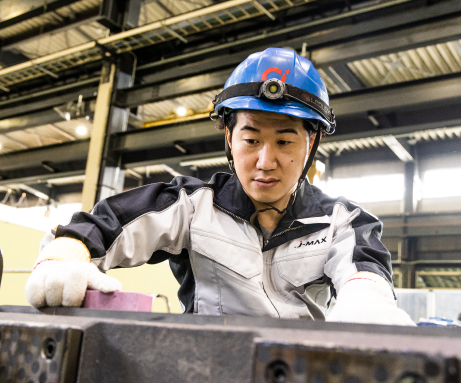
自動車産業発展の一助を担っていることの誇り
入社してよかったことは、自動車の安全性向上、燃費の向上などに確実に活きる仕事ができることです。「スーパーハイテンの冷間加工技術」は他社にはない、当社だけの強み。硬い鉄は成形性に難があって思いどおりにならないのですが、そこに挑戦し続けているのが当社なんです。既存の会社は加工しやすいように、柔らかい素材を成形しています。柔らかいゆえに弱いので、強度を出すために厚みのある材料を使用するため重くなってしまう。それでは意味がないのです。
良い製品は良い金型から生まれる
日本人の真面目さ、繊細な部分が活きるのは、「ものづくり」の場だと思います。その一端を担えることが、とても誇らしいです。私は文系で量産する部署にいたんですが、ずっと「中枢で仕事がしたい」と思っていました。上司からも「当社で仕事をしていくなら金型のことを知らないといけないね」とも。営業志望でしたので「まずは金型を勉強してこい!」という意味でしょうね。日々、戦いです。
当社のコアコンピタンスが金型の製造なので、金型のでき次第で製品の質を左右します。金型でのプレス加工は1分間で20ショットくらい。これが金型の不具合やトラブルで5分停まったら、100ショットのロス。いくら無駄になるでしょうか。私たちの手で金型を作り込まなければならない。「金型を作るのは量産するため」なのですから、いつもそう考えて仕上げをしています。
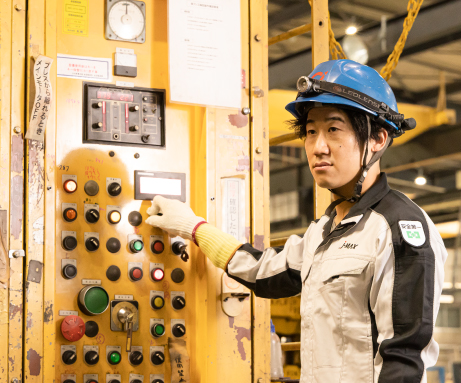
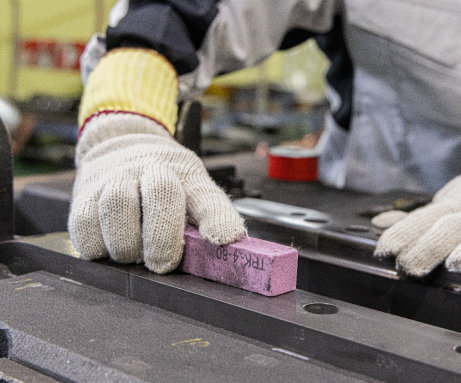
オンオフはきっちり切り替えて楽しむ
繁忙期が終わったら、いつも旅行に行きます。自分の担当している仕事をしっかりやって、休む時はしっかり休むのが信条。韓国など、海外も行きます。海外ドラマも好きで、オフの日に家で観ていることもあります。愛犬と一緒にまったり過ごす日も大切ですね。
学生の方へのメッセージ
- 本気で打ち込める環境だと思います。私自身、「昨日より今日、今日より明日」と毎日思っています。会社のため、自動車産業の発展のために、私の努力が少しでも役に立っていると感じます。特に、ものづくりにおいて金型は必要なツールであり、金型技術の追求に終わりはありません。今後も磨き続けていきます。
また当社は1年に1回、希望する職種を申請するキャリア自己申告シートを提出できます。私も希望を書き込んで今の部署に所属しています。J-MAXは一人ひとりの意見や思いをきちんと吸い上げてくれる会社です。